What are the different types of aluminum finishing?
- Powder coating
- Anodized
- Mill finish
- Wood finish
Aluminum extrusions have been a popular option for many industries. In construction, these materials are used to provide exceptional structural support to many buildings. Other industries like food & beverage, healthcare, and even industrial have also benefited from the numerous advantages of using extruded aluminum profiles. For better enhancement and environmental integrity, these same profiles can also be coated with different aluminum finishing types. Although aluminum is already one of the most advantageous alloys in the market, the added coating gives it an extra boost regarding quality, durability, and aesthetic appeal.
In this article, you’ll have an understanding about some of the most common finishing techniques for aluminum profiles. These can range from powder coating, anodizing, bright dipping, and sublimation. Surface treatment methods drastically impact the quality of the aluminum product positively and allows it to be protected even under duress. Continue reading to learn more.
Powder Coating
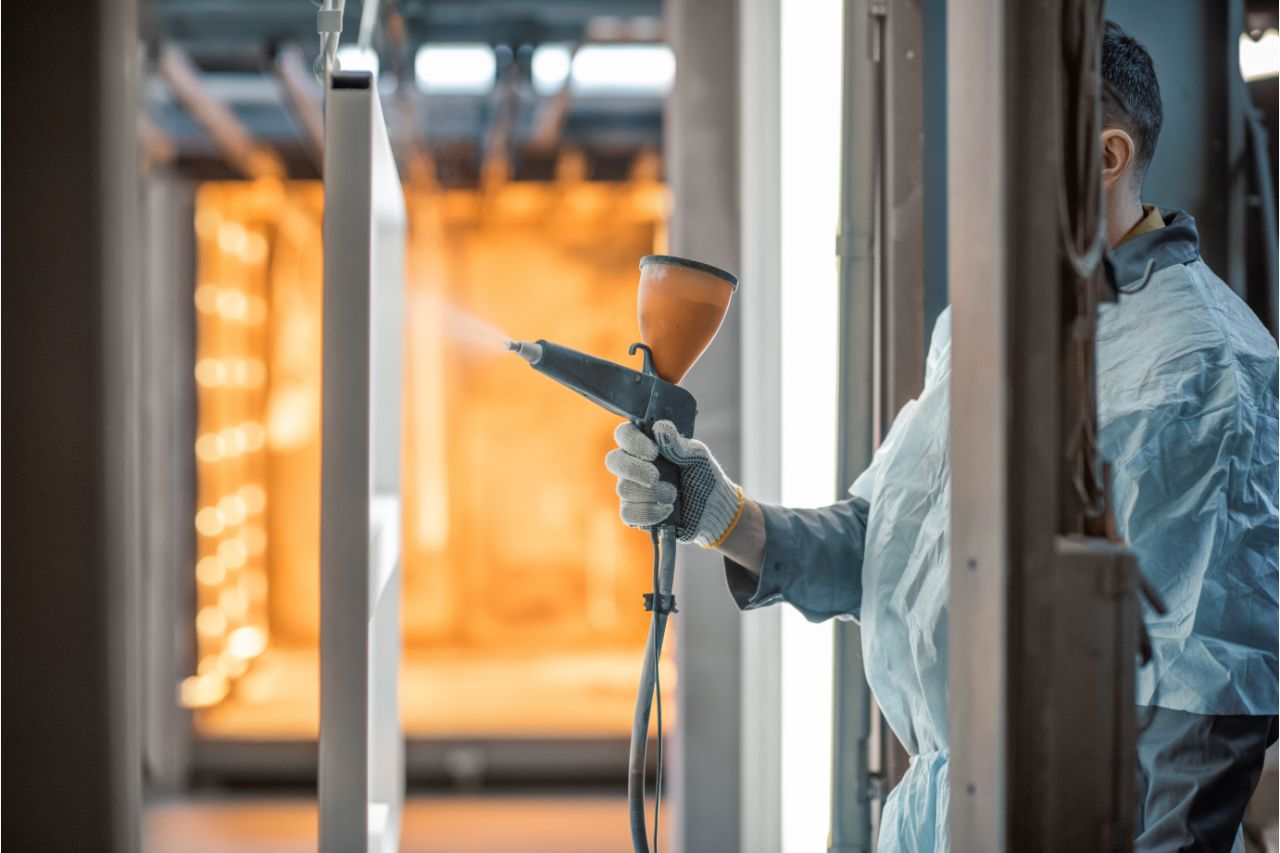
Arguably the most popular choice when it comes to coating aluminum extrusions, powder coating has been a reliable method due to its numerous advantages. Although the look and sometimes texture might be akin to normal paint solvents, powder coating is entirely different, especially with the raw materials involved, method of application, and quality.
In its most basic form, powder coating appears in a dry powder-like compound made out of pulverized resins. In order to allow this coating type to adhere to the surface, it is electrostatically deposited onto the aluminum profile, with the help of chemical effects from additives such as curing agents, levelling agents, pigments, or flow modifiers. Before the finished coated product can be distributed, the initial powder coated material passes through a heat chamber, where the powder is allowed to melt and cool into a seamless and durable finish.
Compared to traditional coating techniques, powder coating has a competitive edge due to its enhanced durability, thicker finishes, eco-friendliness, efficiency, and low waste materials produced. This makes the finish one of the best choices to protect various aluminum extruded parts in the market.
Anodized
Although there may be confusion regarding anodization and powder coating, this is an entirely different method. Where powder coating is an organic form of surface treatment, anodizing is considered as inorganic. Instead of applying a third-party coating form, anodizing focuses on thickening the already-existing natural oxide layer on the aluminum in order to produce a dense film.
Anodized aluminum finishes have been electrochemically coated with aluminum oxide and can be done in a number of ways — batch anodizing and continuous coil anodizing. For batch anodizing, different aluminum accessories are all dipped in an anodizing treatment tank. The length of the submersion will depend on how thick the coating for the part should be, or according to product requirements.
On the other hand, as the name suggests, continuous coil anodizing involves uncoiling raw aluminum as it is subject to different coating stages. The product is continuously anodized, colored, and sealed, making it suitable for high-volume production. Continuous coil anodizing is mainly done on thin-walled aluminum products such as sheets, plates, foil, stamped parts, and the like.
Mill Finish
Unlike the previous types of aluminum coating encountered on this list, mill finish simply refers to bare, factory-formed aluminum that has no applied finishing. Usually, mirror-finished aluminum products or accessories will have a mirror-like quality to them. In some instances, there may also be other visible manufacturing lines that don’t necessarily affect the quality of the product.
Mill finished aluminum can be primed and also coated with liquid paint, but it should first undergo surface preparation by cleaning it with pre-paint prep. Other types of solvent will also work, but the idea is to eliminate the presence of dirt, debris, and other contaminants that may affect the adherence of the coating/primer.
Wood Finish
Wood finishes have also arisen as a formidable alternative to other types of aluminum coating. Although the name may suggest that the aluminum product is coated with a wood-like material, wood finish simply emulates the look and aesthetic appeal of real wood. This presents advantages over real wood, in that the synthetic finishing does not swell, rot, deteriorate, or warp.
Aside from the aesthetic value of wood finished aluminum, the coating is also scratch-resistant and free from corrosion. They also hold up exceptionally well under ultraviolet radiation, making the wood finish perfect for aluminum applications in the outdoors, or wherever it might be exposed to the elements. Some examples would be canopies, pergolas, trellis, column casing, window frames, door frames, and a range of other creative and decorative accents.
Key Takeaway
Powder coating, anodization, mill finish, and wood finish are just some of the many aluminum finishing types that have been widely-used in the industry. Each type of coating has its own benefits.
Overall, all of these coatings can be done for any aluminum profile. Keep these in mind when you’re considering which type of surface layering is most ideal for your aluminum parts, with design, cost-effectiveness, and durability factored in.